New Technology Comes With Potential for New Issues of Corrosion and for Preventative Maintenance
In October 2016, the International Maritime Organization (IMO) established a global limit for sulphur in
fuel oil used on board ships of 0.50% m/m. The “IMO Sulphur Cap” came in to force on 1st January 2020.
Sulphur emissions to the atmosphere by sea-going vessels are now limited by these new international regulations, under the Marpol Treaty. Prior to January 2020, the maximum sulphur cap in fuels was kept at 3.5% m/m. Compliance with the new regulations requires that vessels are either use a more expensive fuel – with low sulphur content – or that they clean their exhaust gases by using Exhaust Gas Cleaning Systems (EGCS)
– commonly referred to as “scrubbers”.
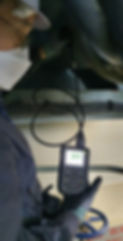
It is left to ship owners themselves how they should comply with the IMO Sulphur Cap (to choose to use more expensive, low sulphur fuel – or install a scrubber system). But, compared to using compliant fuels, it is reported that scrubbers look to be a sound investment as the payback time could be very short (estimated by some to be less than 18 months in many instances).
Therefore, many thousands of ship owners have already chosen to install scrubbers in order to comply with international regulations and standards as economically as possible.
But as the uptake of scrubber technology in the marine sector rises with the entrance into force of the new regulations, corrosion has reared its head as the arch-enemy of these Exhaust Gas Cleaning Systems in the marine environment.
Like with any new technology, scrubber maintenance and operation has been a learning curve for ship owners and operators, especially in the context of preventing failures of the technology and reducing downtime. The wash water from scrubbers, now containing the pollutants it has filtered, is acidic and therefore highly corrosive. The effects of the acidic nature of the wash water on the integrity of the ship is then further aggravated by the high temperatures of exhaust gases. Therefore, the structural integrity of the scrubber and associated pipework will need to be regularly checked for signs of leakage or corrosion; particular areas of interest are the overboard pipe and the “stub piece” in the engine room itself.
One well known ship repair and maintenance company in mainland Europe observes that corrosion of scrubbers is “most definitely an area of concern for us. We continue to see very recently installed scrubbers that are showing obvious signs of corrosion – sometimes in as little as six months from point of installation. As a company that is concerned primarily with preventive maintenance, we certainly recommend regularly checking for wall thickness loss due to corrosion; as the earlier issues are caught, the easier it is for us to deploy and rectify the issue”
Ultrasonic thickness gauging is a simple, inexpensive and reliable method to carry out these checks regularly. Cygnus Instruments (www.cygnus-instruments.com) has specialised in making very robust, accurate and above all “simple to use” ultrasonic thickness gauges for 40 years. The Cygnus range of MK5 gauges all reads through coatings of up to 20mm thick – which means there is no need to remove any of the extremely important (and expensive) protective coatings or epoxy. The first Cygnus gauges were designed for hull inspection work and as such the units are all purpose-designed for a tough life: they are waterproof (IP67), drop proof and shock proof
(US MIL STD 810G standard). Readings taken can be logged and uploaded to simple software in order to be referred to later; thus wall thinning and corrosion can be easily monitored over time and any issues can be
caught and addressed early.
All Cygnus gauges come with a 3 year warranty.
Tel: +44 (0) 1305 265533
E-mail: sales@cygnus-instruments.com